
Or you will need to reuse one of your legacy Solid Edge models. Or you can run an engineering service firm and will need to read a CATIA V5 engine model to guide your tooling design. For example, you design with SOLIDWORKS, but often need to bring components such as a pump in the Creo format by a supplier into the software’s assembly. These three problems have been bothering many more common workflows. The associativity between the original design and derivatives was broken. What would happen if I modified the design? I would have to run the exports and imports all over again, which was the third problem. 3D exports and imports lose data fidelity and can compromise an engineer’s confidence.īy the way, the analysis was supposed to guide my design iterations and optimizations.
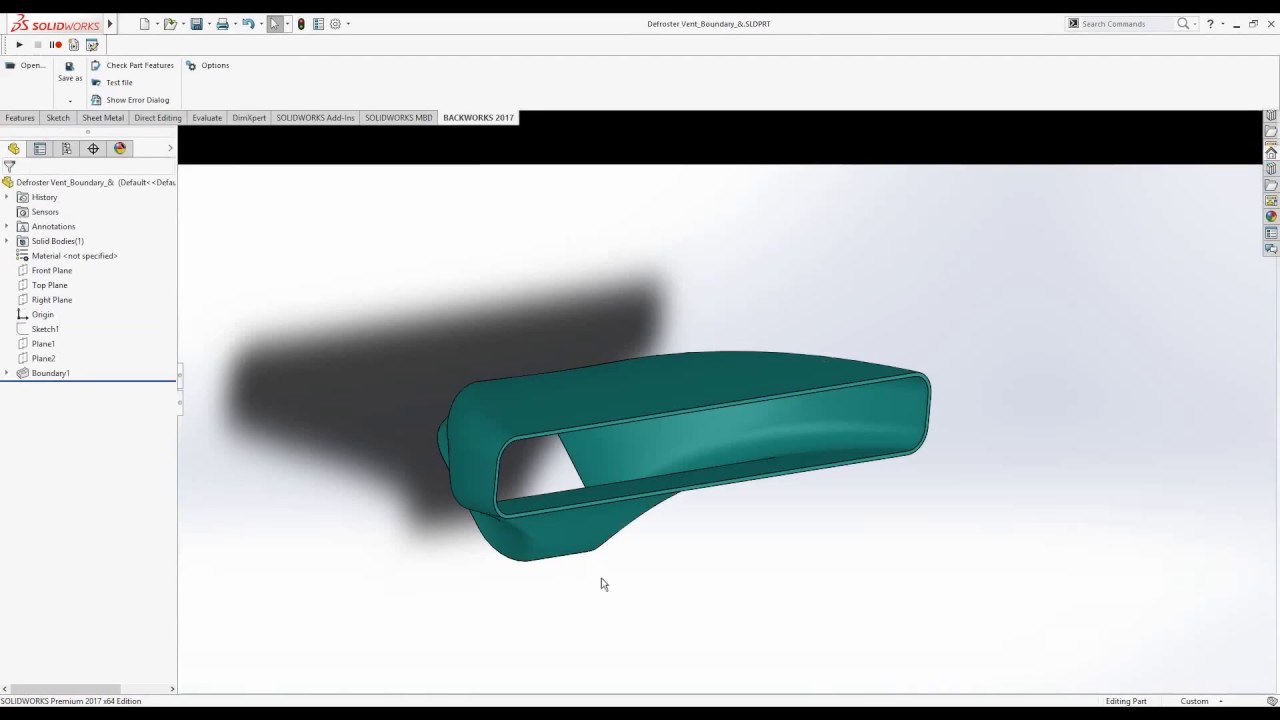
Who knew what could go wrong under the hood? By that time, I really didn’t have much confidence in the translated model or the analysis results. But that was based purely on my visual comparison between them. Then I tried each and every one of them, exporting from one tool and then importing into another with my fingers crossed.Īfter being overwhelmed by all kinds of warning sand missing or redundant geometries during hours of exporting and importing, I finally found a neutral format: x_t, a Parasolid file that presented my model seemingly well from the CAD tool into the analysis software. They all looked like black boxes to me, but I didn’t care that much, either, when I was desperately hunting for a common language that both of my tools spoke. As a young and naïve engineer, I didn’t know what each format meant. What did I try doing to work around this barrier? First, I identified a common subset between the export formats of the CAD tool and the import formats of the analysis software: STEP, IGS, SAT, x_t, x_b… you name it. Oftentimes in design collaborations and data migrations, CAD formats get in the way of the design. I’m sure the tools have evolved a lot in the past 16 years, but the challenge is still there. So there I was, stuck in the middle because the tools didn’t talk to each other. The analysis software available to me at that time didn’t read the CAD format. The result of this analysis was supposed to help me optimize my design.
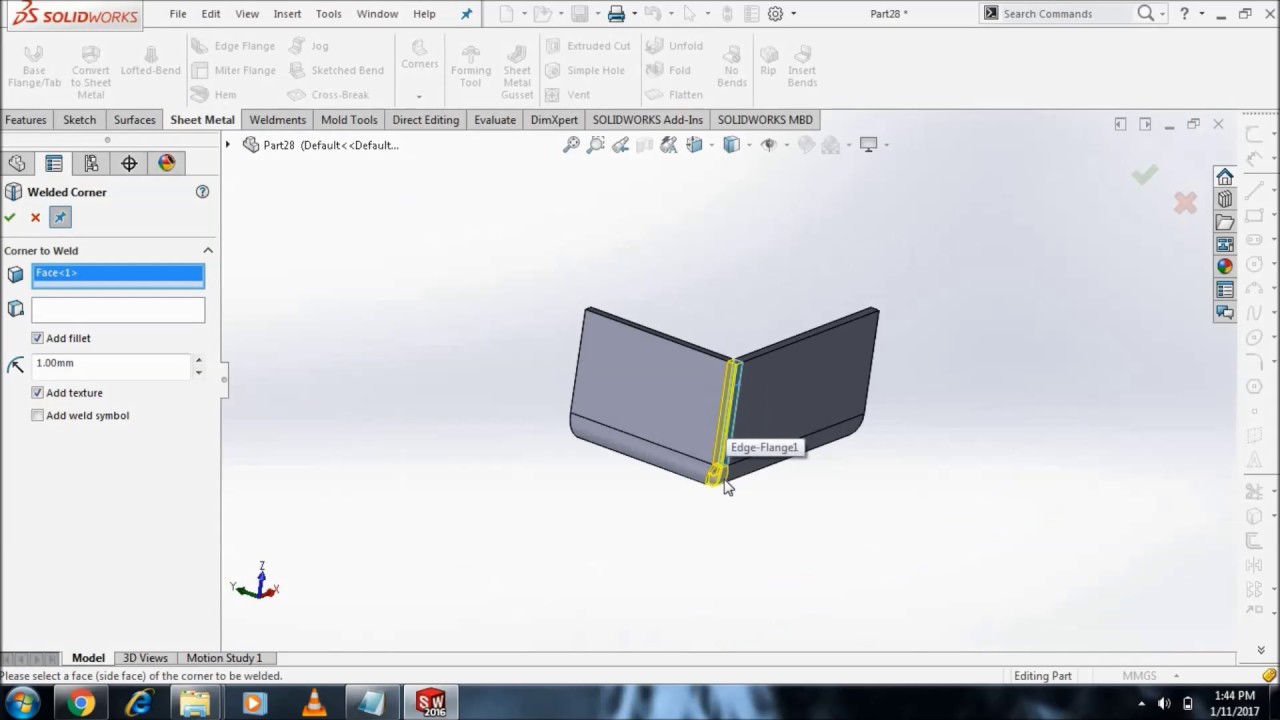
Simply put, the higher these frequencies are and the smaller the amplitudes are, the safer the structure is. In order to avoid any structural damage at common low frequencies, I needed to run a modal frequency response analysis to identify the tray’s first, second and third natural frequencies. Sixteen years ago, I was designing a module tray that supported a gas tank using a CAD tool.
